Dans le domaine industriel, les machines-outils constituent le pilier de la production, qu’il s’agisse de pièces unitaires ou de séries massives. Leur bon fonctionnement est essentiel pour garantir la précision, la sécurité, et la continuité des opérations. C’est dans cette optique que la maintenance des machines-outils se révèle être un enjeu majeur. De la maintenance préventive, qui anticipe les dysfonctionnements, à la maintenance curative, qui intervient en cas de panne, en passant par la modernisation pour améliorer les performances, chaque aspect de ces services est une pièce essentielle de l’efficacité opérationnelle. Dans cet article, nous explorerons en profondeur ces différentes facettes de la gestion des machines-outils, mettant en lumière l’expertise des techniciens, l’importance du contrôle et les avantages de l’entretien.
Maintenance préventive des machines-outils
La maintenance préventive des machines-outils représente un maillon essentiel dans la chaîne de production industrielle. Elle incarne la philosophie de l’anticipation, visant à prévenir les coûteuses pannes et les interruptions inopinées de la production. Dans cette première partie, nous explorerons en détail l’importance de la maintenance préventive, ses composantes clés, et son rôle crucial dans le maintien de la performance et de la sécurité des machines-outils.
Prévenir plutôt que guérir
Au cœur de la gestion des machines-outils, la maintenance préventive occupe une place primordiale. Elle incarne la philosophie selon laquelle il vaut mieux anticiper les problèmes que les résoudre a posteriori. En effet, attendre qu’une machine-outil tombe en panne peut engendrer des arrêts coûteux de la production et des réparations plus complexes. La maintenance préventive se présente comme une solution proactive visant à éviter ces écueils.
En adoptant une approche préventive, les techniciens spécialisés interviennent régulièrement pour inspecter, entretenir et ajuster les machines-outils. Cette vigilance permet de repérer les signes avant-coureurs de dysfonctionnements et de prendre des mesures correctives avant que les problèmes ne s’aggravent. Les avantages sont multiples : une productivité constante, des coûts de réparation réduits, et la prolongation de la durée de vie des équipements.
Les composantes de la maintenance préventive
La maintenance préventive s’articule autour de plusieurs étapes cruciales. Tout d’abord, l’examen périodique des machines-outils est effectué avec minutie. Les techniciens inspectent chaque composant, des pièces mécaniques aux éléments électriques et électroniques. Cette étape permet de détecter les signes de fatigue, d’usure ou de corrosion.
Ensuite, le diagnostic matériel intervient pour identifier les éléments nécessitant une attention particulière. Cette analyse précise contribue à planifier les interventions nécessaires et à commander les pièces de rechange à temps, minimisant ainsi les temps d’arrêt non planifiés.
Enfin, l’analyse des performances des machines-outils permet de garantir leur bon fonctionnement et leur précision. Les techniciens veillent à ce que les équipements respectent les normes de sécurité et de conformité légale, assurant ainsi un environnement de travail sûr pour les opérateurs.
La sécurité et la conformité légale
La sécurité des machines-outils est un enjeu essentiel pour toute entreprise industrielle. Conformément aux réglementations légales, il est impératif de maintenir ces équipements en état de fonctionnement sûr. La maintenance préventive joue un rôle majeur dans cet aspect, en permettant de détecter et de résoudre rapidement tout problème pouvant compromettre la sécurité des opérateurs.
En respectant les normes de sécurité et en assurant la conformité légale, les entreprises peuvent éviter des sanctions potentiellement lourdes. La maintenance préventive n’est donc pas seulement un gage d’efficacité, mais aussi une démarche responsable envers la sécurité de tous ceux qui interagissent avec ces machines-outils.
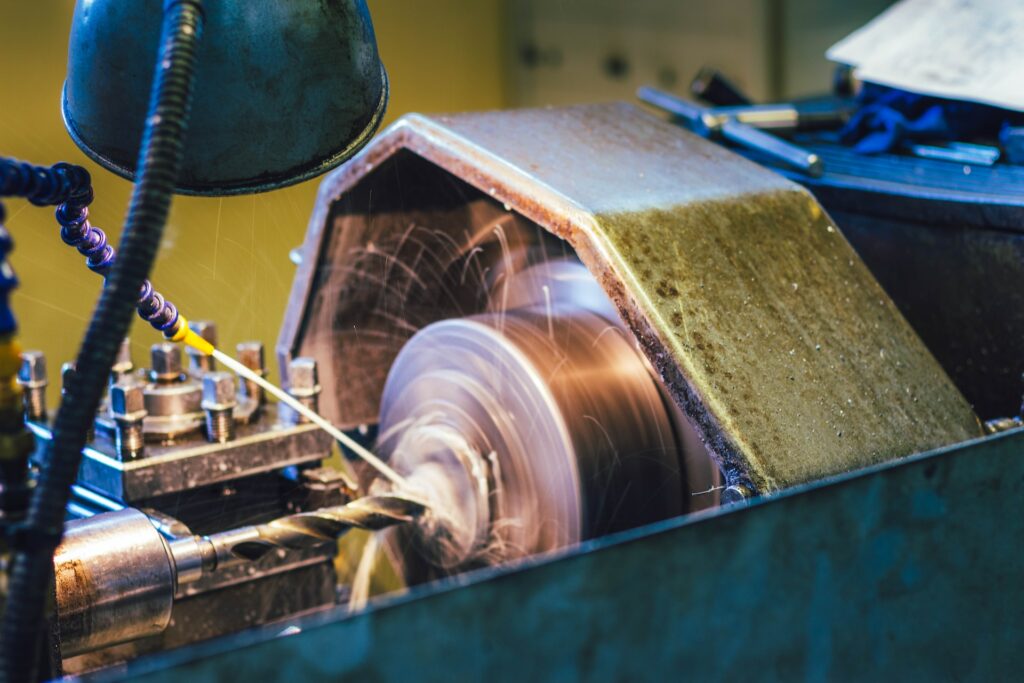
Maintenance curative des machines-outils
La maintenance curative des machines-outils, véritable maillon de secours, entre en jeu lorsque la production est interrompue par une panne inattendue. Elle exige une réactivité inégalée et une expertise technique pointue pour diagnostiquer, réparer et minimiser les temps d’arrêt coûteux. Dans cette deuxième partie, nous plongerons au cœur de la maintenance curative, explorant les compétences nécessaires et les stratégies mises en place pour assurer une remise en service rapide et fiable des machines-outils.
Réparation et dépannage
La maintenance curative des machines-outils prend tout son sens lorsque survient une panne ou un dysfonctionnement imprévu. Les techniciens spécialisés interviennent avec expertise pour diagnostiquer la source du problème, qu’il s’agisse d’une composante mécanique défaillante, d’un dysfonctionnement électrique, ou d’une défaillance électronique. Cette phase cruciale permet de déterminer la nature de l’intervention nécessaire, que ce soit une simple réparation ou le remplacement de pièces défectueuses.
Minimiser les temps d’arrêt des outils de production
Dans un environnement industriel, le temps c’est de l’argent. C’est pourquoi la réactivité joue un rôle déterminant dans la maintenance curative. Réduire au maximum les temps d’arrêt est une priorité absolue. Lorsqu’une panne survient, chaque minute compte. Les techniciens interviennent rapidement, munis des compétences et de l’outillage nécessaires pour résoudre le problème dans les meilleurs délais. Cette approche permet de minimiser l’impact de la panne sur la production et de garantir une reprise d’activité en un temps record.
Expertise technique et connaissances des machines outils
La maintenance curative exige une expertise technique pointue. Les techniciens doivent maîtriser un large éventail de compétences, de la mécanique à l’électronique en passant par l’électricité. Ils doivent être capables de diagnostiquer efficacement la panne, d’identifier les pièces à réparer ou à remplacer, et de réaliser les opérations de dépannage avec précision. Cette expertise garantit une remise en service fiable et sécurisée des machines-outils, contribuant ainsi à la continuité de la production.
La maintenance curative, bien que réactive, repose sur une préparation minutieuse et des compétences techniques avancées. Elle constitue le rempart ultime contre les pannes imprévues, préservant ainsi la performance et la rentabilité des machines-outils dans le contexte industriel exigeant.
Modernisation des Machines-Outils
Dans un contexte industriel en constante évolution, la modernisation des machines-outils s’affirme comme un impératif pour les entreprises cherchant à demeurer compétitives et performantes. Cette troisième partie de notre exploration approfondie se consacre à l’importance capitale de la modernisation, dévoilant les avantages cruciaux qu’elle offre en termes de productivité et de compétitivité. Nous plongerons également dans les différents domaines de la modernisation, de l’électronique à la mécanique, tout en mettant en lumière l’impact de l’automatisation sur l’efficacité opérationnelle.
Enjeux et défi de l’optimisation retrofit des machines industrielles
La modernisation des machines-outils revêt une importance capitale dans le paysage industriel actuel. Elle représente un levier essentiel pour accroître la productivité et maintenir la compétitivité des entreprises. En modernisant les machines-outils, on exploite tout leur potentiel, augmentant ainsi leur efficacité opérationnelle. Cela se traduit par une production plus rapide, une précision accrue, et une réduction des coûts liés à la maintenance et à la consommation d’énergie.
Les domaines de la modernisation
La modernisation englobe une variété de domaines, chacun contribuant à l’amélioration globale des performances des machines-outils. L’électronique occupe une place centrale, avec l’installation de commandes numériques de pointe qui permettent une plus grande flexibilité et une meilleure gestion des processus de production. Au niveau électrique, la modernisation vise à optimiser la consommation d’énergie et à réduire l’impact environnemental. Du côté mécanique, la modernisation implique souvent le remplacement de composants obsolètes par des éléments de pointe, améliorant ainsi la fiabilité et la précision.
L’automatisation des machines de production industrielle
L’automatisation des portes de machines-outils représente une innovation clé dans le domaine de la modernisation. Elle permet une ouverture répétitive des carters de machines-outils, simplifiant ainsi l’accès aux équipements internes. De plus, elle peut être associée à un système de commande automatisé, ce qui facilite la programmation et l’optimisation des cycles de production. Cette automatisation contribue à réduire les temps morts, à augmenter la productivité et à améliorer la sécurité en minimisant les interactions manuelles.
La modernisation des machines-outils s’impose comme un investissement stratégique pour les entreprises désireuses de rester compétitives sur le marché industriel. En exploitant les avantages de la modernisation, elles peuvent accroître leur efficacité, réduire leurs coûts, et s’adapter aux défis toujours plus exigeants de la production moderne.
Cette investigation approfondie de la maintenance, de la réparation et de la modernisation des machines-outils nous a plongés au cœur d’un domaine où la précision, la performance et la sécurité règnent en maîtres. L’évolution constante de l’industrie exige un engagement inébranlable envers l’excellence opérationnelle, ainsi qu’une capacité à saisir les opportunités offertes par la modernisation. La pérennité des entreprises repose sur leur aptitude à maintenir leurs machines-outils à la pointe de la technologie. En demeurant attentifs aux besoins en maintenance préventive et curative, tout en explorant les possibilités de modernisation, les acteurs de l’industrie sont prêts à relever les défis à venir et à prospérer dans un environnement en constante évolution.